ESC Group: Approaching 40 Years as a Global Leader in Construction Solutions
Approaching its 40th anniversary, ESC Group stands as a testament to unwavering innovation, steadfast reliability, and unparalleled excellence. From its humble beginnings in the 1980s, ESC has transformed into a global leader in construction, continuously pushing the boundaries of what is possible in the industry. Maintaining its focus on delivering advanced solutions that meet the evolving needs of its clients across various sectors, including infrastructure, commercial, and marine projects. This growth is a testament to its commitment to quality, cutting-edge technology, and a vision that embraces future possibilities, positioning ESC Group as a beacon of progress and stability in the construction world. Read more….
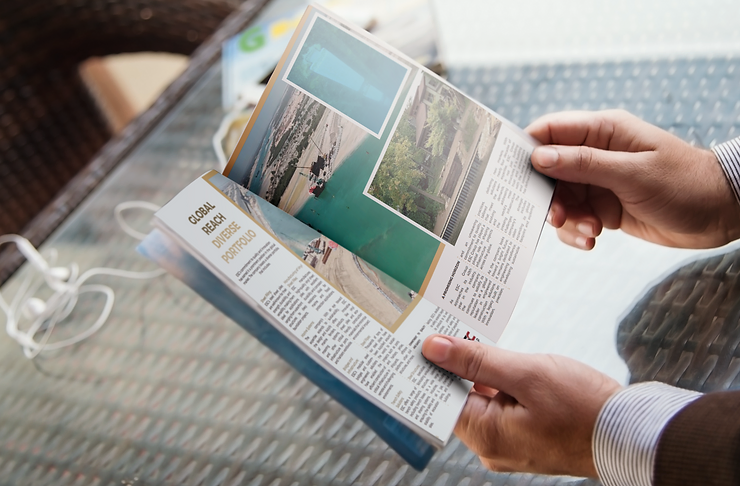
Featured Product: Vinyl Sheet Pile Manufacturing in North Carolina
New Mill for Vinyl Sheet Pile Manufacturing Set to Commence Production in the USA
Statesville, NC – Get ready for a groundbreaking moment! Pietrucha-ESC is stirring the construction world with the announcement of its brand-new, state-of-the-art mill for vinyl sheet pile manufacturing in the USA. This ambitious venture is set to revolutionize the industry, delivering top-tier, locally produced vinyl sheet piles that combine unmatched durability with sustainability.
It’s a bold step forward, meeting the soaring demand for innovative construction materials while shaping a more sustainable future!
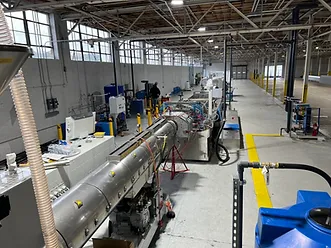
Statesville, NC – Get ready for a groundbreaking moment! Pietrucha-ESC is stirring the construction world with the announcement of its brand-new, state-of-the-art mill for vinyl sheet pile manufacturing in the USA. This ambitious venture is set to revolutionize the industry, delivering top-tier, locally produced vinyl sheet piles that combine unmatched durability with sustainability.
Featured Product: ESC Modular Aluminum Trench Boxes
ESC Trench Safety is proud to announce the launch of its new Modular Aluminum Trench Box System, designed to enhance safety and efficiency in construction and excavation projects.
ESC Modular Trench Box Series is a trench shoring system specially designed for flexibility that allows a variety of configurations suitably as required by users. With its modular structure and aluminum alloy composition, weight is significantly lower compared to steel.
ESC Modular Trench Box is an efficient trenching solution engineered to a high degree of quality and strength, making it an ideal solution for a wide array of excavation and trenching works, particularly quick-phased shoring applications.
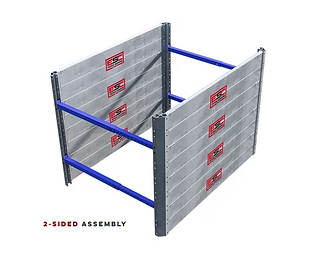
Team Spotlights:
ESC AND MISI CONFERENCE 2024: Highlights from the ESC and MISI Board Meeting in Japan
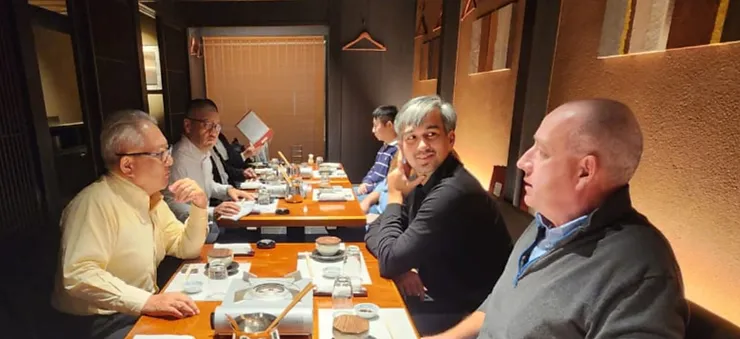
The recent board meeting between ESC Group and Marubeni-Itochu Steel Inc. (MISI) held in Japan was a significant event, bringing together leaders from both organizations to discuss strategic initiatives and future collaborations.
This annual conference provided a platform for in-depth discussions and strengthened bonds between ESC Group and MISI.
ESC PHILIPPINES: Shines at Various Exhibitions
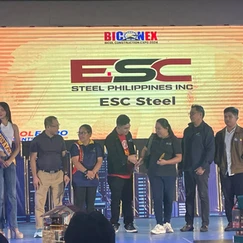

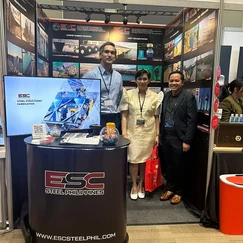
In 2024, ESC Philippines Inc. stormed into five significant events: two construction expos (Biconex and Philconstruct), two civil engineering group events, and one exclusive client event.
CBRE – Supplier Events and Trade Hall Expo 2028 (October 2024)
BICONEX (August 2024)
Philippine Institute of Civil Engineers, Inc. 2024 PICE Midyear National Convention and Technical Conference (October 2024)
PHIL CONSTRUCT Celebrating 35 YEARS (November 2024)
Employee Section:
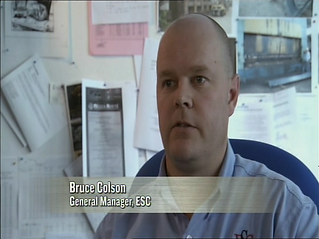
Bruce Colson, first and foremost known as the son of the ESC Group co-founder Mr. Milton Colson, has truly carved out his own legacy since joining the company in October 1993. Starting as a humble Site Supervisor on the JB Landmark project in Johor Bahru, Malaysia, Bruce has risen to become the President of ESC Steel LLC and the ESC Group.
He is now fully committed to propelling ESC’s products and services onto the global stage while instilling a culture of discipline, integrity, and excellence among the staff, all in pursuit of the company’s grand vision and objectives.
Get to know a firm, straightforward, and confident leader, a driving force behind ESC Group and ESC Steel LLC.
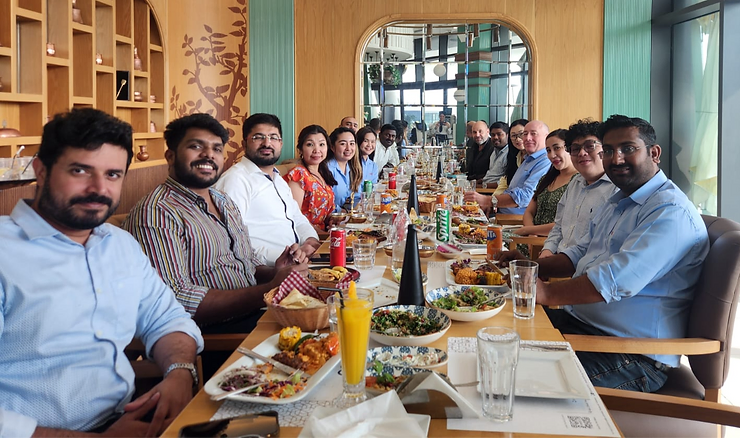
In a day filled with camaraderie and celebration, the ESC Group Middle East team recently gathered to celebrate Kevin Ashdown’s remarkable 30th anniversary with ESC. This milestone event was a testament to Kevin’s dedication and hard work and a celebration of the values and culture that define ESC Group.
Get to know ESC Employees
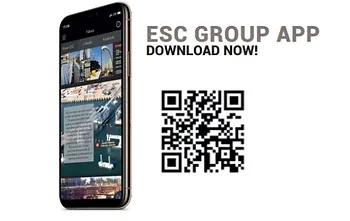