tiam ultricies nisi vel augue. Curabitur ullamcorper ultricies nisi. Nam eget dui elit adipiscing. Etiam rhoncust. Maecenas tempus, tellus eget condimentum rhoncus, Nam eget dui elit adipiscing sem.
What are the Applications of Structural Steel in the Construction Industry?
Structured steel is a category of steel used to create construction materials formed into different configurations, depending on how it’s used. Think of it as the backbone of your construction projects, for it’s incredibly versatile and reliable.
Iron and carbon are two of the main elements of structured steel. The more carbon is added, the greater the strength of the steel. Other chemicals are also added to enhance strength, improve the economics of use and deliver less or more ductility.
Uses of Structural Steel
One of the most important resources in the construction industry is structured steel. Below are its common uses:
Bridges – With thousands or millions of cars passing over bridges, the material used in its construction must withstand pressure stress. One of structured steel’s biggest benefits is that it can be created to significantly improve strength so that it serves its purpose.
Steel Girders, Box Girders, H Girders, Truss Girders, Pipe Arch Girders, Bailey bridge, accessories and other miscellaneous items for bridge construction.
High-Rise Buildings – Structural steel can incredibly resist wind, earthquakes, or other natural disasters because of its strength and flexibility. They will not break under extreme pressure. Also, when building high-rise structures, it’s entirely possible to speed up the construction process with steel.
Industrial Buildings – Structured steel is designed to have a high strength-to-weight ratio and is highly durable. They are also cost-effective, and the pre-made parts are easily assembled. These two factors made structural steel suitable material for industrial structures.
Industrial workshop plants, Processing plants, Power plants
Residential Buildings – Using light gauge steel in residential buildings ensures the structure will last for several years. Also, the flexibility in the structured steel makes them the best material for residential buildings situated near the coast or earthquake faults.
Commercial towers and Public Building– Structural steel is ideal for this type of construction because of its track record of delivering cost-effective and high-quality structures. Structural steel can withstand extreme weather conditions such as rainstorms, hurricanes and earthquakes. They are also adjustable and very flexible.
Depending on the design of the building, the panels can be altered to fit various size requirements. Its versatility allows for more expansion compared to traditionally constructed buildings.
Shopping center, airport terminal, railway station, stadium, museum, art center, theme park etc.
Port Structures and Marine Works – Steel is suitable for port infrastructure and marine structures especially in high design loads however it may corrode when exposed to oxygen and salt water. But it can be minimized so long as there is a planned maintenance system. Also, it’s preferred in these types of structure compared to reinforced concrete due to high labor associated in concrete structure.
Pontoons, Gangways, headstocks, pile heads, mooring dolphins, berthing Dolphins, dredging, Jackets , and accessories, Navigation beacon.
Hydro Power & Wind Farm – Steel is required in these types of construction. Without it, it would not be possible to create a renewable energy source such as wind turbine or hydro power. It plays a crucial role in all renewables especially wind and solar — both require tons of steel.
Penstocks, water gate, trash racks, Pile legs, towers, foundation embedment
Modules & Offshore Platforms – Offshore structures, large oil ducts and drilling structures are made of steel. The usual method is fusion welding where the joining material is the same as the base material.
Marine structure module, processing module, floating module, subsea modules, platforms, risers and jackets.
Steel Structure Fabrication
Fabricating steel is a complex process and should be handled correctly as there are risks involved. Your project’s long-term viability may be compromised when the structured steel doesn’t meet industry standards for composition and tolerances. In the US, steel grades are regulated by ASTM International. It’s crucial that you hire third-party fabricators as they strictly adhere to industry standards.
The fabrication process involves cutting the structural steel, bending, and assembling them. Welding to combine the structures together is also crucial to making the material stronger. The ability to mold and bend steel into a variety of shapes and sections make them the most versatile and cost-effective construction material. It’s also 100 percent recyclable, making them the most sustainable option.
However, it’s essential that you hire the right fabricator. We suggest that you go with third-party steel fabricators as they have more experience and are incredibly competent are fabricating them.
That’s where ESC Steel Structures comes in. We are the top provider of structural steel fabrications worldwide. Our goal is to consistently provide high-quality and timely delivery of our products. Contact us today for a consultation.
Frequently Asked Questions About Structural Steel Fabrication
One of the most widely used metal alloys in the world, steel is important for many uses. Indeed, steel is among the most vital materials for engineering and construction. Structural steel may be used, for example, to construct buildings, bridges and offshore structures, as well as being used in the rail and mining industries. Here are answers to common questions about structural steel.
Bailey Bridge
Known as a portable prefabricated steel truss bridge, Bailey Bridge is extensively used in various applications. Developed and introduced in 1940’s by an English Civil Servant and Engineer, Sir Donald Bailey. Used during the second world war by the British, Canadian, and Military units. The concept behind the Bailey Bridge was to offer a temporary bridge that could rapidly and manually be created in emergency situations.
This was due to its girder and deck systems that can be strengthened at will and constructed without requiring special tools or heavy equipment. The elements and materials should be readily available, not necessarily big and light but flexible. On top of this, they should be strong enough to carry and sustain loads like those of heavy tanks and other machineries.
The bridge boosts socio-economic development by establishing vital connections and delivering supplies, especially to distant areas.
They are instrumental in assisting isolated villages to this day to access larger communities where education and medical resources may be more available. Bailey bridges can assist significantly during humanitarian relief situations to extend help in emergencies brought by natural disasters, war, or terrorism.
ESC Group started offering Bailey Bridge options in 2020 -an add-on to the company’s structural steel division. The success with its fabrication and sales shows great potential in different regions for provisional, makeshift, and permanent bridge structures. Focus will be firstly on Asia and Latin America for sales.
The ESC-HD-100 Bailey Bridge – derived from British 321-Type is suitable for short to medium spans or light to moderate loads.
It can stand to a maximum free span length of 51 meters (167.30 feet), with a deck net width of 4 meters (13.10 feet). The bridge panels are composed of welded high-grade structural steel elements. The girders are lightweight composite panels connected by sturdy steel pins.
Panels and components of the steel bridge are easy to handle and transport can be interchanged. Being lightweight, this bridge type is guaranteed for emergency and difficult situations.
Different configurations and dimensions of bridge panels can also be custom built. They can also be assembled into different forms of panel bridges according to their span length and transportation requirement.
The upgraded version of ESC-HD-100 is the ESC-HD-200 Bailey Bridge. With panel heights increased to 2.13 meters (7 feet), it can cover a maximum free span of 60.96 meters (200 feet) for single-lane width and 45.72 meters (150 feet) for double lane width. In this model, joints between panels are located alternately against the joints between reinforcement chords to reduce inelastic deformation due to oversized pinholes.
Pre-arch or camber is employed to counter deflection of the bridge at the mid-span.
All bolted connections are equipped with orienting sleeves to ensure that compression forces are absorbed by the sleeve and tensions by the bolts. This helps to increase the life span of the bolts and generally the safety of the panel bridge. Composite braces against wind loads are also provided and connected to the transoms or girders to enhance the overall stability of the bridge, especially against side bending.
Nowadays, Bailey Bridge is considered an engineering innovation due to the bridge designs’ continuous modern standardization and modularized nature. Bailey Bridge could be modified based on different span lengths and strengths. True to the original concept, the bridge was also made to be assembled and disassembled as needed.
For more information, you may visit escsteelstructures.ph: Bailey Bridge, Bridge Structures, Pre-engineered Buildings, Port & Offshore Structures, Offshore Platforms, Pressure Vessels, Steel Bridges, Mining Excavation, Steel Towers, Rail Infrastructures, and others.
Structural Steel Applications in Marine Construction
Structural steel has a wide variety of applications in the construction industry. It is one of the most used materials for building various structures. Likewise, structural steel also has a wide range of technical/engineering specifications, such as yield strength, ultimate strength, and ductility.
WHAT IS STRUCTURAL STEEL?
Structural steel is a type of construction material that can be formed into various shapes, depending on the intended use in a particular project. Examples of standard shapes for steel sections are pipes, tubes, angles, channels, and wide flange sections. These shapes can be used for different parts of a structural framing, such as beams, girders, purlins, and columns.
There are also different methodologies on how to create the previously mentioned steel sections. Two of these methods are hot-rolled, and built-up sections. Hot-rolled sections refer to structural steel being rolled from the mill in a monolithic manner. Built-up sections on the other hand are structural sections that can be formed into the specified shape by welding steel plates together.
Some of the commonly used shapes for structural steel shall be discussed in the succeeding sections.
STEEL PIPES
In marine construction, steel pipes are usually used as infill elements for a sheet pile wall. In between two sheet pile panels, a pipe is installed to provide a higher section modulus, which provides better resistance against lateral loads being applied to the wall during its useful life.
Steel pipes can also be used as foundation elements for wharf and pier structures. These pipes are driven to the ground until it reaches a competent subsurface layer to provide adequate support to these offshore structures.
STEEL H and W SECTIONS
Similar to steel pipes, wide-flange (W) and H sections can be used for offshore/marine applications. Most of the time, these shapes can be designated as beam and girder elements of a bridge framing system. These serve as main flexural members of the bridge and shall resist various gravity and lateral loads such as traffic loads, earthquake, and wind loads. W and H steel sections are also used as walers for retaining wall structures. Interconnected walers act as a continuous beam to evenly distribute forces from the sheet piles to the steel struts.
W and H sections are effective as beam elements due to its shape: the flanges contribute to high section modulus values, while having a reduced mass per unit length as compared to other structural shapes.
STEEL SHEET PILES
Steel sheet piles are commonly used in offshore applications as a water-retaining and earth-retaining structures. Offshore construction such as cofferdams, jetties, and quay walls often require steel sheet piles to form the wall components. Like steel pipe piles, sheet piles are driven into the ground at its most optimum design depth to provide overall stability of the structure. Sheet piles are connected using steel interlocks at its ends to form a continuous wall. The interlocks are then applied with a sealant to prevent any water seepage when the sheet piles are installed at the sea.
OTHER STRUCTURAL STEEL APPLICATIONS
There are other structural steel shapes/sections that can be fabricated, as necessary. For special structures, non-standard shapes are usually required by the structural engineer to satisfy the desired flexural and shear capacity of the structure.
ESC Steel is a leading global supplier of fabricated structural steel sections. The capabilities of the in-house engineers and other technical professionals have led the company to working on a wide range of steel construction projects in a global scale.
Should you need structural steel for marine construction, or anything else, click here to get in touch with us today. We are always happy to help.
Steel-Concrete Composite Construction
Principle
Construction materials of different properties are combined to interact and respond against loads in synchronization rather than individually. These composite materials are physically connected to utilize their distinct strengths and features to form a single unit stronger than any separate parts.
Steel-Concrete Composite Construction is meant to achieve efficient and lightweight structural solutions for construction and other related industries.
Background
This engineering and construction method has been widely practiced over a century ago, more dominantly involving the steel-concrete connection. Concrete-encased steel sections were initially developed as composites with the purpose of overcoming the effects of fire while ensuring stability against axial and bending forces.
Composite columns with reinforced concrete core and steel pipe or steel tubular shell were introduced to provide an integral and permanent formwork. Profiled galvanized metal sheets were also introduced to eliminate traditional formworks and at the same time, increasing the strength of reinforced concrete slabs.
Standards
- Design of composite beams and composite slabs for buildings are covered by BS EN 1994-1-1
- Design of Composite Steel and Concrete Structures are covered by BS EN 1990-1999 Eurocode 4
- Australian Bridge Design Code, Section 6: Steel and composite construction
- BS 5400 British Standard code of practice for the design and construction of steel, concrete and composite bridges
- ASHTO: Standard Specifications for Highway Bridges; 24 CFR 200 Sub-part S
- Concrete Slab Stresses in Partial Composite Beams and Girders, American Institute of Steel Construction, Vol. 21
Applications
Composite construction is extensively used in bridges, multistorey buildings, warehouses, marine structures, and more. Many applications in the mentioned structures are categorized as beams & girders, floor systems, and column systems.
Composite Beams and Girders. Composite beam includes a steel section in I or W shape attached to a concrete slab by shear connectors atop of it. They have been recognized as one of the most economical structural systems for both multistorey buildings and bridges.
Obviously, building and bridge floors should be stiff and massive enough to reduce deflection and vibrations. In this case, reinforced concrete is undoubtedly the material of choice. The supporting beam or girder, however should have a superior strength-weight ratio, a quality that only steel can offer.
Composite Floor Systems. Composite floor system consists of steel beams, profiled metal decking, and reinforced concrete slab. These materials are combined in a compact and very efficient way to form a profile that is basically designed to hold gravity or dead loads as well as traffic loads.
Composite floor systems are mostly used as bridge decks and floor slab for wide range of building classifications largely for elevated car parks and multistorey commercial buildings
Composite Column Systems. Composite columns can either be concrete-filled steel tube or concrete-encased steel element. Either way, composite columns are advantageous as follows
- Flexural resistance of steel pipe or tube is maximized when provided with concrete infill
- Steel casing prevents spalling and confines the concrete.
- Concrete infill delays local buckling of the steel casing and enhances compression resistance
- Steel casement replaces formwork and reinforcing steel
Advantages
The success and versatility of composite construction can be stated in a simple and straight forward explanation – concrete responds excellently in compression and steel behaves the same in tension.
Joining the two materials together as a structure, these strengths can be used to achieve a highly efficient and lightweight design that can effectively resist both axial and flexural forces. Other benefits and advantages are as follows:
- Composite systems are over 25% lighter than concrete construction. As a result, site erection and installation are easier, and labor costs can be minimized.
- Steel-concrete composite can have high strength from a relatively small cross-sectional area.
- The reduced weight of composite itself reduces the forces in those elements supporting them. In this way, supporting members including foundation costs can also be reduced.
- Superior strength-to-weight ratio of composite materials allows compact designs which are expected to be aesthetical, economical, safe, and green.
- Composite systems eliminate the costly activities of traditional concrete forming like propping, stripping, and other temporary works.
- Steel and concrete can be arranged to produce an ideal combination of strength according to calculated requirements.
- Concrete-encased steel elements has good resistance to buckling, fire, and corrosion.
- Composite beams can cover longer spans without the need of intermediate columns, thanks to steel.
- Composite columns reduce the requirement of lateral reinforcement and time-consuming fixing of lateral ties, as well as providing easier connection to steel beams of a steel-framed structure.
- Composite columns involving steel tube or pipe casing simplifies foundation works and construction in bodies of water.
- In marine construction, pouring of concrete under water is made possible by applying composites. Driven steel pipes and sheet piles serves as integral and permanent formworks for concrete infill.
- Concreting of succeeding floors may proceed without having to wait for the previously cast floors to gain strength. The steel decking system provides positive moment reinforcement for the composite floor, requiring only small amounts of temperature bars to control cracking.
Summary
The benefits of combined steel-concrete construction are characterized by three major aspects: speed, performance, and value.
- Steel-concrete composite is about 30% lighter than reinforced concrete and slightly heavier than structural steel by 2%. This significant reduction in weight of composite materials compared to reinforced concrete along with the elimination of huge amount of false works contributes to a huge factor in reducing construction timelines.
- With concrete being strong in compression and steel in tension, the combination of the two materials has proven and excellent results in enhancing the structural performance of the product composite unit. Application of steel-concrete composite can increase the maximum shear strength of a floor slab by 85% according to the results of a study by ASCE.
- Overall savings using steel-concrete composite can be as high as 10% compared to reinforced concrete and 7% when compared to structural steel. Steel encased with concrete does not only improve the strength of the composite members but protect the entire structure from adverse effects of fire, calamities, and corrosion.
Why Consult ESC?
ESC Steel Structures is one of the top providers of structural steel fabrications around the world.
ESC’s capabilities include Steel Bridge Structures, Bailey Bridge, Pre-Engineered Steel Buildings / Pre-Fabricated Steel Buildings, Offshore Steel Structures, Mining and Excavation Structures, Pressure Vessel Fabrication, Steel Towers, Rail Infrastructures, Material Handling Structures, and more.
Please find us at www.escsteelstructures.ph ✉️ philippines@escpile.com 📞+63 920 504 3801
Performance of Steel Buildings against Natural Disaster
Having sufficient knowledge of the latest and applicable design codes and standards enables a structural engineer to prepare cost-effective and safe design solutions for different structures. In essence, structures like concrete and Steel Buildings must be designed to resist the forces applied in various combinations/loading conditions. This is especially true for project sites where Natural Disasters such as storms/typhoons and earthquakes occur frequently.
Four (4) basic load cases are considered when designing Steel Buildings. The first two are predominantly applied along the gravity direction, while the succeeding loads are predominantly applied in the lateral direction. Further explanation of these basic load cases are as follows:
Dead Loads (D)
Dead loads are loads applied to the structure along the gravity direction. These include the self-weight of the structure (all permanent construction), and other materials permanently fastened onto the structure.
Live Loads (L)
Live loads are also applied along the gravity direction. These are loads are calculated depending on the structure’s occupancy. Live loads may vary at different locations of the structure. For example, the magnitude of the live load for an office space/room shall be different from that of the storage area of a particular building.
Wind Loads (W)
Wind loads are a combination of lateral and vertical loads applied to the contact surfaces of the building. Calculation of the wind load for a specific structure considers several factors. The structure’s geometry, the maximum wind speed at the project site, exposure category, gust effect, directionality and topography are just some of the major factors to be considered when designing Steel Buildings.
Earthquake Loads (E)
Earthquake/Seismic loads are forces calculated due to the seismic events the structure will be subjected to. Factors such as the nearest seismic source, the magnitude of the earthquake, soil type, and the type of seismic force-resisting system to be used are some of the factors to be considered in the calculation of the design earthquake loads for a structure.
The basic principle of structural design is to select the best section of a structural member that can safely and economically resist the loads applied to it. These loads include various combinations of gravity and lateral forces in accordance with the provisions of the referral code. A structural steel section is considered economical if it can resist loads while maintaining an optimum self-weight (usually expressed in mass per unit length). An optimized self-weight of the section implies that lighter steel sections are required to be fabricated, and effectively lowers the material cost. At present, there are two design philosophies that are being used when designing steel structures. These are the Allowable Stress Design (ASD) Method, and the Load and Resistance Factor Design (LRFD) Method.
In the Allowable Stress Design Method, the steel section to be selected shall have cross-sectional properties (i.e., area and moment of inertia) adequate to resist the maximum applied loads under a permissible value. Applied loads may be in the form of compressive or tensile axial forces, shear forces, bending moments, and torsion. Each form of the applied load is compared to a permissible value of sectional strength.
This permissible value is referred to as the Allowable Strength. The Allowable Strength is defined by taking the Nominal Strength of the steel section and dividing it by a Factor of Safety (FS).
The value of FS varies for different types of loading conditions. For example, the safety factor for bending moment capacity shall be different from the factor of safety for shear capacity of the section.
In the Load and Resistance Factor Design, the sectional strength of a member under failure conditions is considered. The design process under LRFD is done by taking the sum of applied service loads and multiplying it with an individual load factor for each load type. The factored loads are then applied to the structure. Member size selection is determined by calculating for the strength of the chosen steel section and multiplying it by a reduction factor. To illustrate this better, the working principle behind LRFD is expressed as follows:
Factored loads are usually greater than the service loads, thus making the load factors greater than 1.0. The factored strength is always less than the nominal strength of the steel section, thus making the resistance factor less than 1.0.
At this point, the discussion focused on the determination of the sectional strength of a structural member. Despite satisfying the strength requirements from the applied loads, serviceability is also an important criterion in determining the right design for a structure. Two of the most common factors to consider in serviceability are the member deflection and the story drift. Depending on the governing design code, the deflection criterion is satisfied by taking the maximum deflection of a structural member due to the applied loads, and comparing it with the allowable deflection prescribed in the code. The allowable deflection is expressed as a fraction of the member’s unsupported length. This fraction also varies depending on the load condition being considered (e.g., D only, L only, D plus L).
The second factor being considered when checking for serviceability is the drift of the structure. Drift is defined as the lateral displacement of the building when subjected to load combinations involving transient loads (wind and earthquake loads). In practice, the drift is calculated at the beam-column joints of the structure, per floor. The displacement of a joint on one story relative to one below it is called the inter-story drift.
For service load combinations involving wind loads, the permissible inter-story drift is valued as H/600 to H/400, where H is the story height. The permissible value is referred from Appendix CC (Serviceability Considerations) of ASCE 7-16 (Minimum Design Loads for Buildings and Other Structures).
For service load combinations involving earthquake/seismic loads, the seismic inter-story drift shall be not greater than 2.50% of the story height being considered for structures having a fundamental period of less than 0.70 s. For structures with a fundamental period of 0.70 s or greater, the seismic inter-story drift shall not be greater than 2.00% of the story height under consideration. The seismic drift is inelastic in nature due to the inelastic response of the seismic force-resisting system. The inelastic drift is calculated using the following equation:
Where Δm is the inelastic drift, R is the seismic response modification factor, and Δs is the elastic drift. The prescribed drift limits were based on studies that determine the tolerance of both structural and non-structural elements of a uilding against lateral displacements under seismic events.
It is important that safety and economics are considered when designing Steel Buildings of any material type (i.e., reinforced concrete, structural steel, or a combination of both). These two factors should go hand in hand to come up with efficient building designs of varying occupancies. Adequate sectional strength and serviceability limits as prescribed by the local/governing structural codes must be observed by the Structural Engineer, especially for areas frequently struck by Natural Disasters such as earthquakes and strong typhoons. Strict implementation of these referral design codes ensures the optimum performance of the building while maintaining the safety and welfare of the general public.
For expert assistance on your steel building structures requirement, contact our team. You may email us at info@escsteelstructures.com or visit our website https://www.escsteelstructures.ph/ for further information
Application of Structural Steel in Bridges
Structural Steel Bridges exist in significant numbers in every corner of the world. In the United States alone, more than 30% of the Bridges are built with Steel as the exclusive or major component. Steel Application in Bridges are not just strong, durable, and flexible, they are extremely beautiful. Many of them are popular as magnificent attractions, historical landmarks, ‘Nobel Prize’ winners, and valuable architectural masterpieces.
Structural Steel as a solution to extensive bridge projects guarantees lighter and faster construction, innovative designs, socio-economic benefits, and positive environmental effects. As a versatile material, Structural Steel components can be fabricated into limitless formations to cater all bridge types and designs. They can be basically arches, trapezoidal, helical, and more; or maybe in complicated shapes such as a knot, a serpentine torch, and other irregular figures. These materials possess the flexibility to create wonders like the stunning neo-futuristic steel structures we see around us nowadays. Vast application of Structural Steel is evident in different types of Bridges as follows:
Beam Bridges
Designed primarily for function and efficiency, this type supports reinforced concrete deck slabs using steel ‘I-beams’ resting on abutments or piers at each ends. There are two types of beam Bridges: multi-girder involving multiple steel beams; and ladder deck – consist ing two steel beams and intermediate bracings. They are suitable for highway Bridges of medium span (13m to 100m). Recently constructed Beam Bridges have decks rigidly connected to the abutments for the purpose of eliminating expansion joints and bearings. Beam or stringer Bridges are the simplest and does not much consider aesthetics.
Box Girder Bridges
This is a type of bridge with beams shaped like a hollow rectangular or trapezoidal box also called the ‘box girder’. A box girder consist two webs joined at the top and bottom by flanges, in some cases it is closed at the top by the deck itself. They are usually built from pre-stressed concrete, Structural Steel, or a composite of steel and reinforced concrete. The cross-sectional configuration of a box girder is ideal for applications requiring good torsional stiffness such curved Bridges and other difficult design cases. Box girder Bridges are appropriate for spans of 100 to 200m using either a single box or more as required. When utilized for lengths of over 200m, they are likely to function as integral part of a cable-stayed or suspension bridge. Photo credit: pinterest.co.uk
Truss Bridges
Load-bearing capacity of a truss bridge depends on the framework of its superstructure composed of interconnected steel elements forming triangular units. The purposeful orientation of each individual steel member contributes to the efficiency of the truss to perform in tension, compression, or both as a result of dynamic loads.Trusses also serves as beam or component in composite decks, as arch bridge stringers, as cantilever beams, or as girders to cable-stayed Bridges. They are widely applied in foot-Bridges, demountable Bridges, gantries, and railway Bridges of over 50m span.
Arch Bridges
A ‘through arch bridge’ is also known as a ‘half-through arch bridge’ or ‘through-type arch bridge’. An arch structure which can be a steel truss, plate box girder, steel I-beam, or reinforced concrete section, supports the bridge deck. The deck can be supported on struts, sit on top of the arch, or suspended from the arch by tension cables. Steel arches act primarily in compression. Variation of this bridge type is the ‘tied-arch’ or ‘bow string arch bridge’. The deck hangs from the arch above it and acts as a tension tie. Arch Bridges are well suited to abridge wide waterways or wherever foundation works are difficult to construct or establish. Aside from being architecturally attractive, these Bridges are relatively cheaper and flexible. Photo credit: en.wikipedia.org
Suspension Bridges
Typical suspended Bridges are built with two steel cables hung between two supports forming a catenary. For short span structures such as a footbridge, the steel cables are replaced with alternative material say an arch steel pipe. The bridge deck is suspended from these cables by a series of vertical high-tension wires along its length. All of the steel cables and hangers absorb tension forces. Suspension Bridges are used as solutions for longest spans. One of the most iconic examples of a suspension bridge is the famous Golden Gate Bridge of San Francisco, USA
Cable-stayed Bridges
Cable-stayed bridge involves towers or pylons where high-tension cables are anchored to support the deck girder at intervals. The cables or stays run directly from the tower throughout the center or both sides of the deck resembling a fan-like pattern. This type of bridge is an optimum solution for spans longer than Cantilever Bridges but shorter than Suspension Bridges. Recent engineering advances have made it possible to extend the effectiveness of Cable-stayed Bridges up to spans of over 1 kilometer. The anchor towers, which can be in the form of A-frame; H-frame; or a column, works in compression. The deck girders sustain compression and bending stresses.Photo credit: en.wikipedia.org
ESC Group’s ESC Steel Structures division has a global supply capability of heavy Structural Steel bridge products. It is the ESC policy to fabricate and furnish clients with quality products to international standards. ESC has completed major bridge projects around the world – and is an expert in steel bridge girder and arch fabrication.
The types of Bridges within ESC’s capabilities include:
- Steel highway Bridges
- Railway Bridges
- Movable Bridges – eg Bascule, Swing
- Heavy truss structures
- Multiple plate girders
- Trapezoidal box girders
- Suspension Bridges
- Steel Arch Bridges
- Temporary or Modular Bridges
- Special Bridges
Other components that ESC can fabricate include:
- Handrails
- Steel columns
- Decking Formwork
- All types of bridge bearings
Should you have a requirement, you may contact our expert. Email us at info@escsteelstructures.com
Safety Aspects of Structural Steel
Structural steel has long been one of the most utilized materials in different magnitudes of many fabrication and construction works. Steel structures can be an integral part or almost the entirety of Steel Bridges, Pre-engineered/ Prefab Steel Buildings, Offshore Structures, Heavy Steel Fabrication Units, Pressure Vessels, Material Handling Structures, and more.
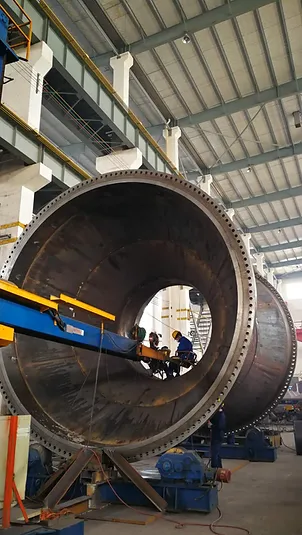
While studies and discussions have shed light on aspects of cost, strength and durability, and speed of installation, many are still skeptical about the advantage of structural steel in terms of safety.
There are features of steel itself and behaviors as a structure which has positive influence to safety.
Here is to explain some of the most notable among them.
- Structural steel and reinforced concrete both produce structures that are strong enough to withstand fire, strong winds, heavy snows, termites, and fires. However, steel structures have the most significant advantage over concrete structures when comes to behaving against earthquakes.
- Besides earthquakes, steel framed structures perform better against natural phenomena such as hurricanes and snow loads, and man-made circumstances like explosions. The extraordinary tensile strength of steel is the reason behind it.
- Steel is non-combustible and does not ignite nor spread flames. This property helps a steel structure to prevent rapid spread of fire and sudden collapse. Although steel loses strength when exposed continuously to extremely high temperatures, it gives warning as it buckles or deflects before finally crashing. That moment, which can be as fast as a blink of an eye, or a couple of seconds, means everything in a matter of life and death.
- Steel structures are conductible or well-grounded and are less probable to be hit or damaged by lightning. A steel-framed building permits lightning current to pass harmlessly through the steel members then into the ground. Materials with greater resistance to electricity are more likely to absorb structural damage when struck by lightning. A steel building with a properly installed lightning protection system is safe against that fearsome 1,000,000 volts of electricity.
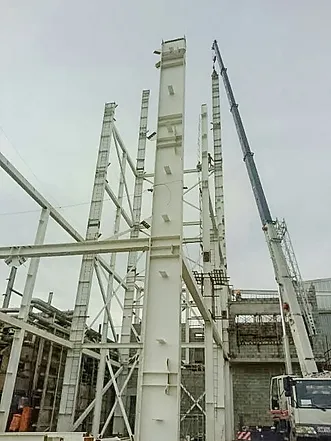
- Labor works using steel solutions can be reduced up to over 50% compared to other alternatives. The lesser work force employed at a given project, the lesser lives are exposed to danger. Risks and hazards associated to heavy congestion and traffic at work areas are also eliminated.
- Pre-fabricated steel building solutions appears to make construction time significantly shorter. The shorter duration to complete a project also means lesser time of exposure to hazards. Pre-fabrication of multiple structural steel elements in controlled environments not only promote quality but minimizes works at heights. Because steel components are delivered to the site as assemblies, minimal number of workers and timeframe is required to finish the installation.
- Recycling is a process that enhances environmental safety. Steel is the most recycled material at present with at least 80% of its kind generated from recycled products. Steel can be recycled repetitively or can be reused without further processing. Steel is a greenhouse material contributing to not just the safety of a team of workers or a group of building occupants but the planet Earth.
- Quality assurance check on steel structures is an easier task to perform because all members are exposed and accessible. This is essential when integrity of structures, after occurrence of any kind of phenomena, must be assessed whether capable to safely continue its service or not
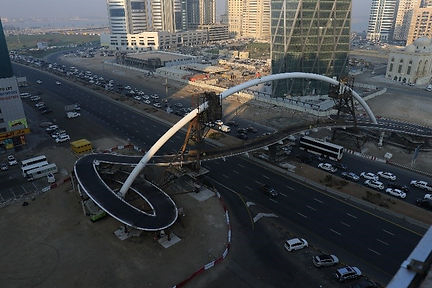
Some experts claim that the overall performance of any building against seismic activity is more a function of design rather than the material used in construction. However, structural steel is obviously becoming a top choice of designers and owners because of its promising properties and characterristics.
Do not take chances, seek for professional assistance! Please contact us at info@escsteelstructures.com visit our website www.escescsteelstructures.com.